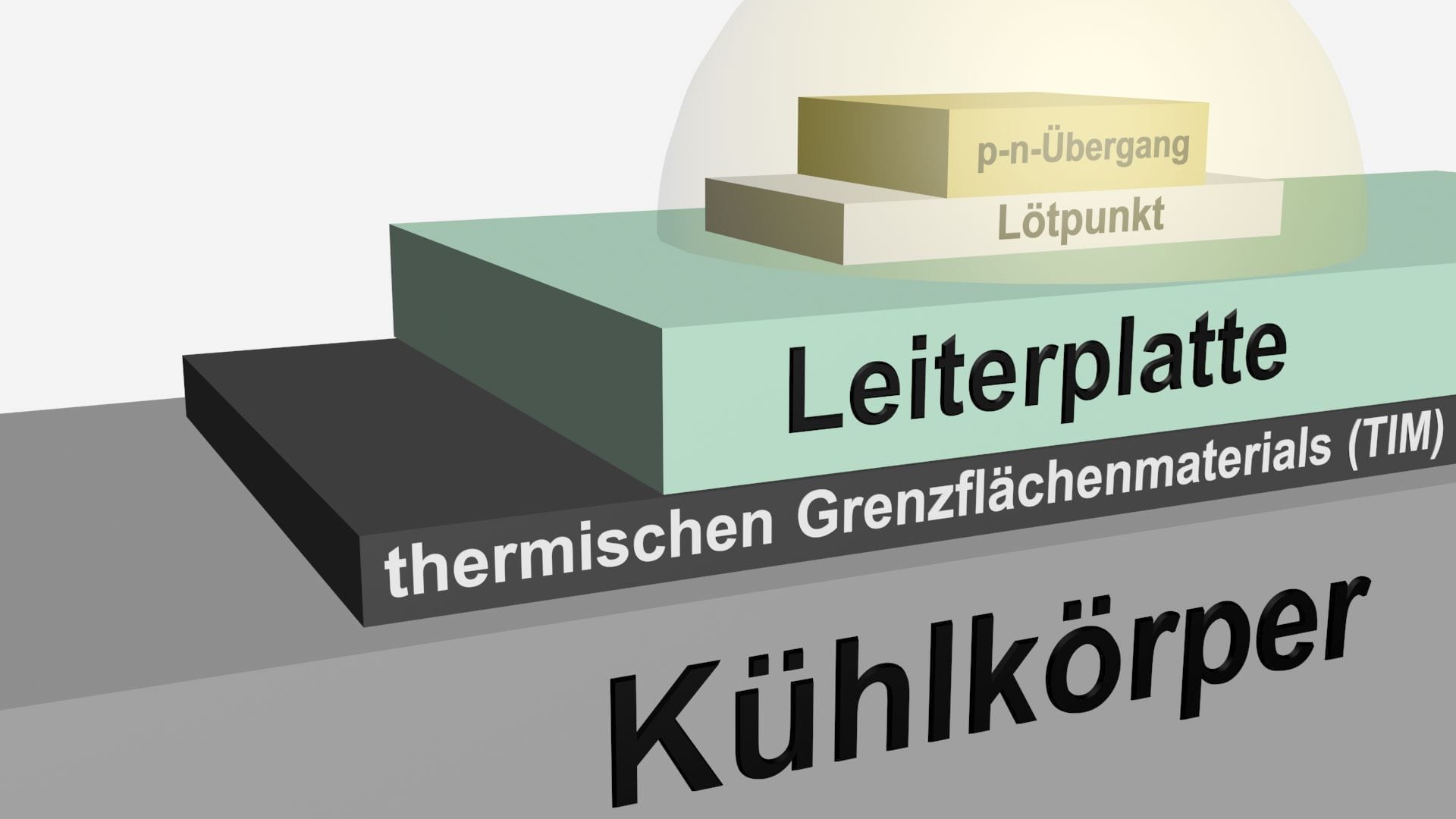
Los diodos emisores de luz de alta potencia (LEDs de alta potencia) pueden ser de 350 milivatios o más fuertes en un solo LED. La mayor parte de la energía en un LED se convierte en calor en lugar de luz (aproximadamente 70% de calor y 30% de luz). Si este calor no puede ser disipado, los LEDs brillan a temperaturas muy altas. Esto no sólo disminuye la eficiencia, sino que también acorta la vida útil del LED. Por lo tanto, la gestión térmica de los LEDs de alta potencia es un área esencial de investigación y desarrollo. Es necesario limitar la temperatura de unión de un valor que garantice la vida deseada del LED.
Transferencia de calor
Para mantener una temperatura baja de la capa de la cerradura que mantenga la alta potencia de un LED, cualquier posibilidad del retiro del calor de los LED debe ser considerada. La conducción de calor (reducción), la remoción de calor por aire (convección) y la radiación son las tres posibilidades para la transferencia de calor. Típicamente, los LEDs están encapsulados en una resina transparente, que es un mal conductor de calor. Casi todo el calor generado se pasa a través de la parte posterior del chip. El calor es generado por la transición p-n por la energía eléctrica que no se ha convertido en luz útil. Alcanza el punto de soldadura a través de una larga distancia desde el punto de conexión, el punto de soldadura a la placa de circuito y la placa de circuito al disipador de calor y luego se dirige a la atmósfera del entorno externo.
La temperatura de la capa de barrera es menor si la impedancia térmica es más pequeña o la temperatura ambiente es menor. Para maximizar el rango de temperatura ambiente utilizable para un rendimiento de pérdida determinado, se debe minimizar la resistencia térmica total desde el punto de conexión al entorno.
Los valores de resistencia térmica varían ampliamente dependiendo del material y de los componentes adyacentes. Por ejemplo, RJC ( capa de barrera de resistencia térmica a la carcasa) oscila entre 2,6 ° c/W y 18 ° c/w, dependiendo del fabricante del LED. La resistencia térmica del material de conducción térmica (también TIM: material de interfaz térmica) también varía en función del tipo de material seleccionado. Los TIMs guying son epoxi, pasta térmica, adhesivo y lote. Los LEDs de alta potencia se montan a menudo en placas de circuito de núcleo metálico (MCPCBs) conectadas a un radiador. El calor pasado a través de la placa metálica del módulo y el radiador termoconductor es entonces disipado por convección y radiación. Además del diseño y del diseño del cuerpo de enfriamiento, la uniformidad superficial y la calidad de cada componente, la presión, la superficie de contacto, el tipo de material de la conducción termal y su grueso son. Estos son parámetros para la resistencia al calor o enfriamiento del LED a través de la extracción de calor.
Enfriamiento pasivo
Los factores de enfriamiento pasivo para una gestión eficiente del calor de los LEDs de alta potencia son:
Conductor térmico
El conductor térmico se utiliza normalmente para conectar el LED a la placa y la placa al radiador. El uso de un conductor térmico puede optimizar aún más la salida de calor.
Disipador de calor
Los disipadores de calor contribuyen significativamente a la eliminación de calor. Funciona como un conductor que dirige el calor desde la fuente LED hasta el medio exterior. Los disipadores de calor pueden deducir energía de tres maneras: conducción de calor (reducción: transferencia de calor dentro o de un sólido a otro), convección (transferencia de calor de un sólido a un fluido en movimiento, para la mayoría de las aplicaciones LED es El fluido el aire ambiente) o radiación (transferencia de calor de dos cuerpos de diferentes temperaturas superficiales a través de la radiación térmica).
- Material:
La conductividad térmica del material que conforma el radiador afecta directamente el rendimiento de la pérdida de la conducción térmica. Normalmente, el aluminio se utiliza debido a la muy buena relación calidad-precio. En el caso de los refrigeradores planos, el cobre se utiliza a menudo, a pesar del alto precio de compra. Los nuevos materiales incluyen termoplásticos, que se utilizan cuando los requisitos de disipación de calor son más bajos de lo normal (por ejemplo, a menudo en los requisitos del hogar) o formas complejas en el proceso de fundición por pulverización tienen sentido. Las soluciones de grafito a menudo tienen una transferencia de calor más eficaz (no la conducción térmica) que el cobre con un peso más bajo que el aluminio. El grafito se considera una solución de enfriamiento exótica y es más costoso de producir. También se pueden añadir tubos de calor a refrigeradores de aluminio o de cobre para reducir la resistencia a la dispersión.
- Forma:
La transferencia de calor tiene lugar en la superficie del enfriador. Por lo tanto, los disipadores de calor deben diseñarse para tener una gran superficie. Esto se puede lograr mediante el uso de un gran número de costillas finas o mediante la ampliación del propio radiador.
Aunque un área de superficie más grande conduce a un mejor rendimiento de enfriamiento, debe haber suficiente espacio entre las costillas para crear una diferencia de temperatura considerable entre la costilla de enfriamiento y el aire ambiente. Si las costillas están demasiado cerca el uno del otro, el aire en medio puede tener casi la misma temperatura que las costillas, por lo que no se realiza ninguna transferencia de calor. Como resultado, más costillas de enfriamiento no conducen necesariamente a más energía de enfriamiento.
- Textura:
La radiación térmica de los enfriadores es una función de la textura superficial, especialmente a temperaturas más elevadas. Una superficie pintada tiene un mayor nivel de emisión que una superficie brillante y sin barnizar. El efecto es más notable para los refrigeradores superficiales, donde cerca de un tercio de calor es disipado por la radiación. Además, una superficie de contacto plana óptima permite el uso de una pasta de conducción térmica más delgada, lo que reduce la resistencia al calor entre el disipador de calor y la fuente LED. Por otro lado, la anodización o el grabado también reducen la resistencia térmica.
- Método de instalación:
Los sujetadores del cuerpo de enfriamiento con tornillos o plumas son a menudo mejores que los clips convencionales, el conductor térmico o la cinta. Para la transferencia de calor entre las fuentes del LED sobre 15 vatios y los refrigeradores del LED, se recomienda utilizar un alto-calor que conduce el material de interfaz (TIM) que tiene una resistencia térmica sobre la interfaz de menos de 0,2 K/W. Actualmente, el método más común utilizado es un material de cambio de fase que se aplica a temperatura ambiente en forma de almohada sólida, pero luego se convierte en un líquido gelatinoso grueso tan pronto como se eleva por encima de 45 º C.
Tubos de calor y cámaras de vapor
Las tuberías de calor y las cámaras de vapor tienen efectos pasivos y sus capacidades de conductividad térmica son muy efectivas de 10.000 a 100.000 W/mK. Ofrecen las ventajas siguientes en la gerencia de calor del LED:
- Transporta el calor a otro radiador con una mínima caída de temperatura
- Isothermizes control de calor a través de convección natural, aumentando la eficiencia y reduciendo su tamaño. Es un caso conocido en el cual la adición de cinco pipas de calor redujo la masa del Conflux del calor por el 34% de 4,4 kilogramos a 2,9 kilogramos.
- El alto flujo de calor directamente bajo un LED eficientemente en un flujo de calor más bajo, que puede ser disipado más fácilmente.
PCB (apretado: placa de circuito presionado)
- Mcpcb:
MCPPCB (PCB de núcleo metálico) son tableros que contienen un material de metal base para la distribución de calor como una parte integral de la placa de circuito. El núcleo metálico generalmente consiste en una aleación de aluminio. MCPCB tiene la ventaja de una capa de polímero dieléctrico con una alta conductividad térmica.
- Separación:
La separación del circuito del conductor LED de la placa LED impide que el calor generado por el conductor aumente la temperatura de la capa de bloqueo del LED.
Recubrimiento de platino
- Proceso aditivo:
En los PCB, las sustancias conductoras se aplican al material portador durante el proceso de producción para la creación de una superficie estructural conductiva. El conductor sólo se aplica a la imagen de pista del conductor predeterminado. Por el contrario, esto se encuentra grabado en el proceso sustractivo. Básicamente, hay una conexión directa con el radiador de aluminio; Por ejemplo, no se requiere ningún material adicional para la conexión térmica para el circuito. Esto reduce las capas conductoras de calor y la superficie térmica. Se reducen los pasos de procesamiento, los tipos de materiales y las cantidades de material.
Placas de escalera de aluminio (también conocidas como placas de circuito IMS para sustratos metálicos aislados)-aumenta la conexión térmica y proporciona una alta tensión de penetración dieléctrica. Los materiales toleran el calor hasta 600 ° C. Los circuitos se unen directamente a sustratos de aluminio, por lo que no se requieren materiales de conducción térmica. La conexión térmica mejorada puede reducir la temperatura de la capa de bloqueo del LED hasta 10 ° C. Esto permite al programador reducir el número de LEDs requeridos en una placa aumentando el rendimiento de cada LED. También puede reducir el tamaño del sustrato para cumplir con las limitaciones dimensionales. Se ha comprobado que una reducción en la temperatura de transición aumenta considerablemente la vida útil del LED.
Factor de forma
- Viruta del tirón:
El chip LED se monta con el frontal hacia abajo en el soporte, que generalmente se hace de silicio o cerámica y se utiliza como un distribuidor de calor y sustrato portador. La conexión de la FLIP-viruta puede ser eutéctica, con plomo, sin plomo o el trozo de oro. La fuente de luz primaria proviene de la parte posterior del chip LED. Una capa reflectante se construye generalmente entre el emisor de luz y los sitios de soldadura para reflejar la luz emitida hacia abajo. Varias compañías utilizan cajas flip-chip para su LED de alta potencia, reduciendo la durabilidad térmica del LED en aproximadamente 60%. Al mismo tiempo, se mantendrá la confiabilidad térmica.